From the Works in Progress Newsletter: The wonder of modern drywall, by Yassine Meskhout.
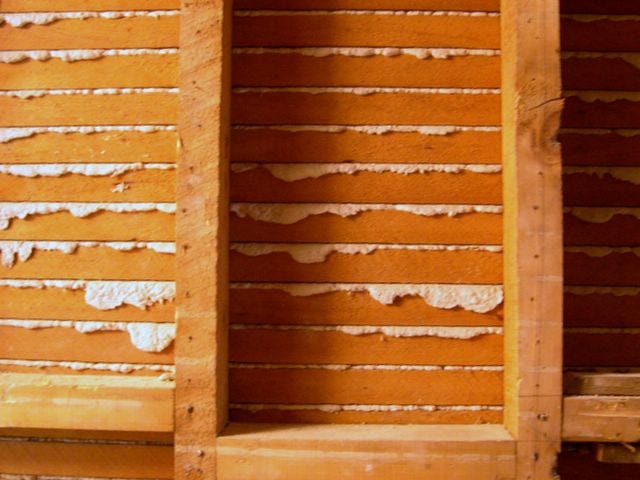
There’s a very old building technique, going back at least 6000 years: construct a lattice of sticks and plaster it with mud (“wattle and daub”). The more recent version is called “lath and plaster”:
The tried-n-true technique of slathering a moldable workable paste onto a rigid canvas as a way of constructing walls has barely budged across eons. Even past the industrial revolution, the cutting edge technique at the turn of the 20th century was plaster-n-lath. Instead of random sticks, you use uniform wooden strips. Instead of dirt, you use plaster made out of gypsum — a mineral known for its fire resistance. Same, but different.
The problem with slathering paste to make walls is that it is a skilled trade and incredibly labor-intensive. Creating a plaster wall on top of a lath canvas was done in-situ, and required multiple coats, each with its own drying time. You slather, then wait for it to dry, then slather on again, then wait for it to dry again. The walls of a typical home would take a skilled plasterer a week or two to make. The end result was either ok at best, or a wobbly warped mess. You are fighting against gravity after all.
Drywall is a big improvement over lath and plaster:
Drywall, also known as gypsum board or plasterboard, is essentially a rigid panel made by pressing a thick layer of familiar gypsum plaster between two durable sheets of heavy paper. This creates a strong, smooth, and easily paintable surface that forms the backbone of most modern interior walls and ceilings. Developed in the early 20th century, it wasn’t until the 1950s that drywall rapidly took over as the standard for walls and ceilings in American homes.
Superficially, drywall looks the same as and is made of the same stuff as a plaster and lath wall. While both are a hardened layer of gypsum powder, drywall sheets are manufactured en masse off-site, in large factories under tightly controlled conditions for consistency and efficiency, then shipped to construction sites ready to install. Instead of a plasterer working his damnedest to ensure straightness across a 12-foot tall canvas of paste, gypsum powder is trivially extruded into uniform shapes, sandwiched by protective layers of heavy-duty paper, like an inedible ice cream sandwich. Cheap, uniform, and free of defects.
More
Comparing Process Improvement in Manufacturing and Construction: Duco vs. Drywall. Brian Potter, Construction Physics, November 2022. Potter notes that drywall still has limitations: “Drywall can at best be regarded as a partial solution for the time-consuming finishing process for a building’s interior walls. While an improvement over the previous plastering process, installing drywall is still a time-consuming, multi-day process. Applying the joint compound (which covers edges and imperfections in the panel) is typically done over several days, as multiple layers of compound are applied and dry.”